Experience Sharing
2025 Quarter 1 Issue 53
Robotic EOAT applications
EOAT stands for End of Arm Tooling, meaning the gripping device at the end of the robot arm. In the highly automated modern industrial production, the robot is an inevitable core equipment. Its performance and efficiency directly determine the overall performance of automation applications. EOAT, as a key actuator between the robot and the workpiece, is an important factor in improving production efficiency and ensuring product quality. It features diverse types, flexible access methods and wide application fields, and it is commonly used by robot to enable different fetching methods and testing applications, and is a very important technical links in the field of industrial automation.
There are many ways for robot to pick up parts, and the way of gripping parts mainly depends on the shape, material, weight and working environment of the product. The commonly used ways of picking parts include clamping, vacuum suction, holding, fastening, digging, magnetic suction, internal bracing and combination of above.
Clamping: used for workpiece with easy to clamp shapes. Can use sprue grippers or parallel grippers for clamping, sometimes together with silicone sheet or foam to prevent scratch mark on products and with magnetic switch for clamping detection.
Vacuum suction: used for picking flat and smooth surface plastic parts. It uses the negative pressure and the suction cup to grip the workpiece. When multi-parts need to be picked can use multiple vacuum circuits/vacuum cups. It normally uses digital vacuum pressure switch for gripping detection.
Holding: This method generally uses two or more groups of cylinders, adjustable spacing design, to make a set of fixture to pick similar size and the same type/shape of products, suitable for larger, heavier and not easy to deform products, such as barrels and baskets. It normally uses magnetic switch or contact switch for gripping detection.
Digging: usually applied to parts which have undercut and not able to pick out directly. It needs digging design to pull out the undercut area of the part before moving out. Such kind of products include mobile phone covers or special caps. It normally uses magnetic switch or photo sensor for gripping detection.
Magnetic picking: used for metal workpeice. It uses magnetic gripper for picking and most commonly used for picking insert parts. It normally uses photo sensor or proximity switch for gripping detection.
Internal bracing: used for workpiece with specific shape and structure, especially ring shape or hollow structure parts. It is suitable for picking parts which have complex shapes, rugged surfaces or not allowing to be picked by grippers or vacuum cups due to surface requirement. Internal bracing can prevent touching the product surface and prevent any scratch of damage to the surface.
Combination of above gripping methods: used for complex shape or special workpiece. When part picking needs to use more than one above picking methods.
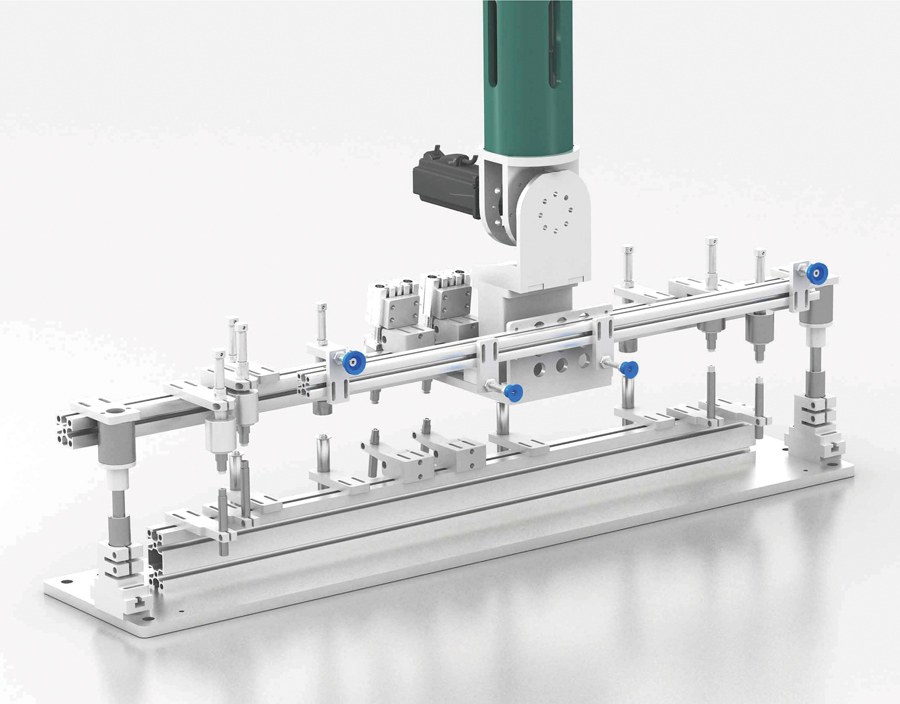
EOAT application illustration
There are many ways for robot to pick up parts, and the way of gripping parts mainly depends on the shape, material, weight and working environment of the product. The commonly used ways of picking parts include clamping, vacuum suction, holding, fastening, digging, magnetic suction, internal bracing and combination of above.
Clamping: used for workpiece with easy to clamp shapes. Can use sprue grippers or parallel grippers for clamping, sometimes together with silicone sheet or foam to prevent scratch mark on products and with magnetic switch for clamping detection.
Vacuum suction: used for picking flat and smooth surface plastic parts. It uses the negative pressure and the suction cup to grip the workpiece. When multi-parts need to be picked can use multiple vacuum circuits/vacuum cups. It normally uses digital vacuum pressure switch for gripping detection.
Holding: This method generally uses two or more groups of cylinders, adjustable spacing design, to make a set of fixture to pick similar size and the same type/shape of products, suitable for larger, heavier and not easy to deform products, such as barrels and baskets. It normally uses magnetic switch or contact switch for gripping detection.
Digging: usually applied to parts which have undercut and not able to pick out directly. It needs digging design to pull out the undercut area of the part before moving out. Such kind of products include mobile phone covers or special caps. It normally uses magnetic switch or photo sensor for gripping detection.
Magnetic picking: used for metal workpeice. It uses magnetic gripper for picking and most commonly used for picking insert parts. It normally uses photo sensor or proximity switch for gripping detection.
Internal bracing: used for workpiece with specific shape and structure, especially ring shape or hollow structure parts. It is suitable for picking parts which have complex shapes, rugged surfaces or not allowing to be picked by grippers or vacuum cups due to surface requirement. Internal bracing can prevent touching the product surface and prevent any scratch of damage to the surface.
Combination of above gripping methods: used for complex shape or special workpiece. When part picking needs to use more than one above picking methods.
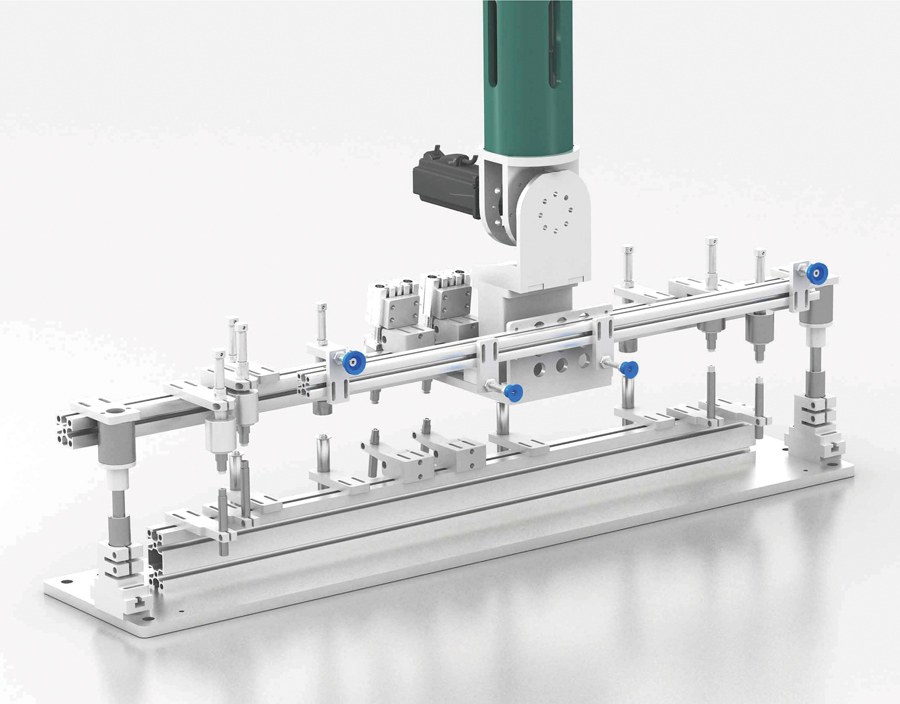
EOAT application illustration
The detection application of an EOAT mainly involves the detection of various parameters and states of the workpiece it picked, so as to ensure the accuracy of the robot operation and the quality of the workpiece. Commonly used detection involves position detection, force detection, state detection, quality detection and intelligent detection.
Position detection: use photoelectric sensor, proximity sensor and other position detection devices to monitor the real-time position of the workpiece. The detected position information is compared with the preset reference position to determine whether there is any deviation, and the operation of the robot is adjusted accordingly.
Force detection: prevent the workpiece from being damaged or falling off due to the clamping force being too large or too small. The clamping force to the workpiece is monitored by the force sensor in real time. The detected clamping force is compared with the preset clamping force range to ensure that the clamping force is within a reasonable range.
State detection: real-time monitoring of workpiece and clamping status, in order to timely detect and troubleshoot any abnormalities. By installing different sensors on the EOAT to monitor the states of the workpiece and the gripping device, and then send the state information to the control system, it can allow the control system to adjust the robot or trigger alarm accordingly.
Quality detection: when the workpiece is gripped and moved to the assigned position, you can use inspection device (e.g. visual system…) to inspect the workpiece and see if it is OK or NG.
Intelligent detection: use integrated sensors, controllers and intelligent algorism to allow the robot to sense and analyze the condition of the workpiece, and adjust automatically according to the received information. Such intelligent detection not only increased the accuracy and efficiency of detection, but also lower the cost and risk of human intervention. Through the technological development of the robot and the EOAT, such kind of intelligent detection will be more and more popular.
There are many ways for different combination of robot and EOAT to pick up parts, and each has its own features. In practical application, the appropriate fetching method should be based according to the specific situation and working environment of the workpiece being picked. At the same time, through advanced detection technology and equipment, the accuracy and stability of the robot operation is ensured, so as to the improved production efficiency and product quality.
Position detection: use photoelectric sensor, proximity sensor and other position detection devices to monitor the real-time position of the workpiece. The detected position information is compared with the preset reference position to determine whether there is any deviation, and the operation of the robot is adjusted accordingly.
Force detection: prevent the workpiece from being damaged or falling off due to the clamping force being too large or too small. The clamping force to the workpiece is monitored by the force sensor in real time. The detected clamping force is compared with the preset clamping force range to ensure that the clamping force is within a reasonable range.
State detection: real-time monitoring of workpiece and clamping status, in order to timely detect and troubleshoot any abnormalities. By installing different sensors on the EOAT to monitor the states of the workpiece and the gripping device, and then send the state information to the control system, it can allow the control system to adjust the robot or trigger alarm accordingly.
Quality detection: when the workpiece is gripped and moved to the assigned position, you can use inspection device (e.g. visual system…) to inspect the workpiece and see if it is OK or NG.
Intelligent detection: use integrated sensors, controllers and intelligent algorism to allow the robot to sense and analyze the condition of the workpiece, and adjust automatically according to the received information. Such intelligent detection not only increased the accuracy and efficiency of detection, but also lower the cost and risk of human intervention. Through the technological development of the robot and the EOAT, such kind of intelligent detection will be more and more popular.
There are many ways for different combination of robot and EOAT to pick up parts, and each has its own features. In practical application, the appropriate fetching method should be based according to the specific situation and working environment of the workpiece being picked. At the same time, through advanced detection technology and equipment, the accuracy and stability of the robot operation is ensured, so as to the improved production efficiency and product quality.
Experience Sharing
- We innovate to secure a large order of mould temp. controllers
- A very interesting project led by Adrian Kaninski from Plastigo
If you want to read other articles, back to2025 Quarter 1 Issue 53.