Experience Sharing
2023 Quarter 2 Issue 50
Reliable Energy Saving with centralize system solution
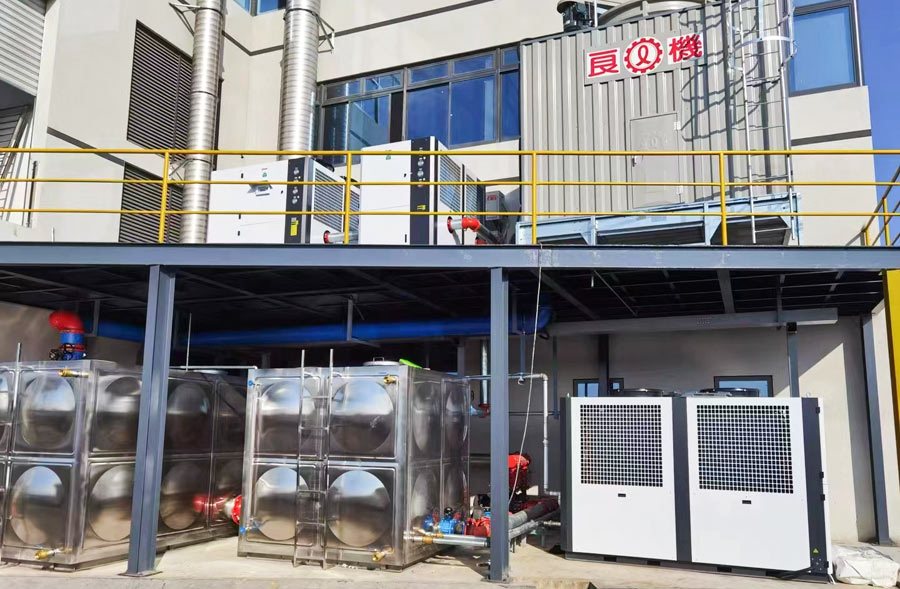
Dual-temperature Coordination - Central Water System
In this design, the water-supplying system is designed outdoors, covering a working space of 30 sqm. It adopts two decks of vertical steel platforms to reduce the overall footprint. Two stainless insulated water tanks are placed on the left side of the lower deck, storing room temperature water and chilled water, respectively. The air-cooled central water chiller works on the right. The original two air-cooled water chillers work at the platform's upper deck. It enhances the whole system’s working stability. In addition, it installs a square exhaust vent on the top of the chiller’s cooling fan and reserves sufficient space to ensure an excellent heat-ventilated environment for the chiller.
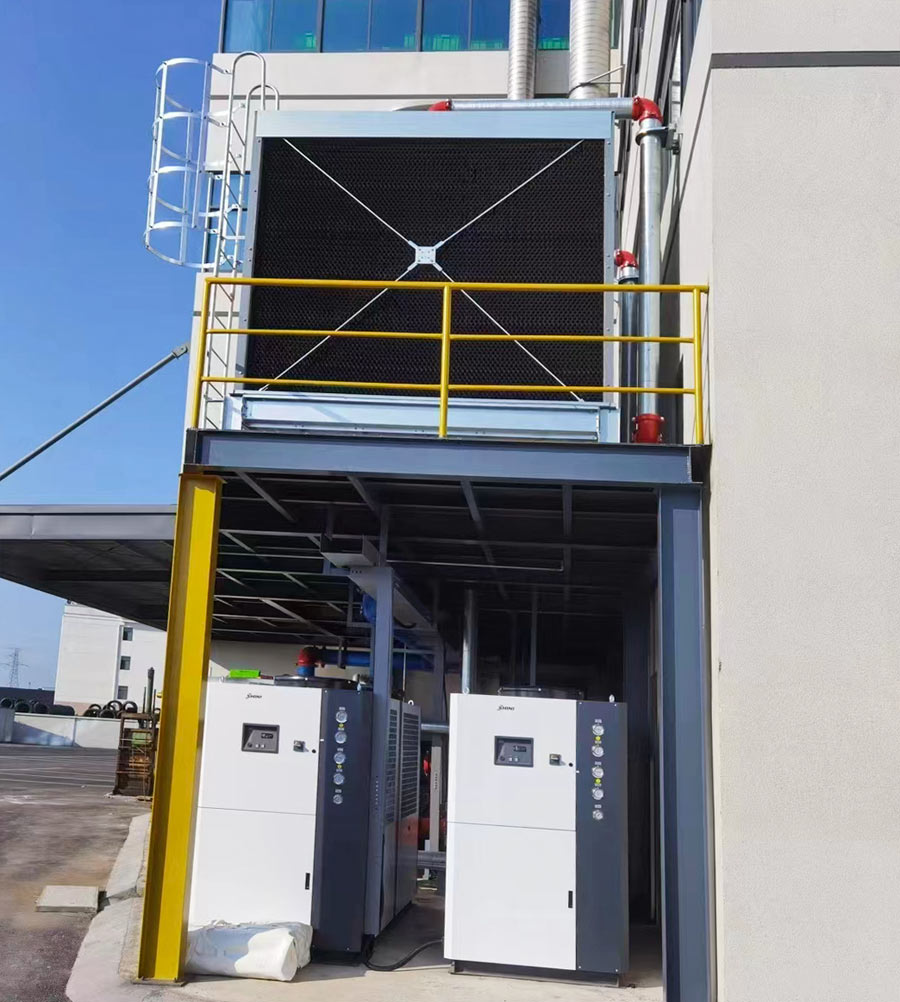
A square cross-flow cooling water tower is installed above the platform and connected to the lower water tank by pipelines. The return water in the workshop will flow to the cooling water tower after filtering by a self-cleaning filter, and it will enter the water tank after cooling and be stored.
Place the water system control box inside the platform, and it can automatically control the pump opening frequency and quantity according to the water demands of the workshop based on an excellent controller algorithm to achieve the energy-saving effect. Meanwhile, the pump works alternately to improve the service life and system reliability.
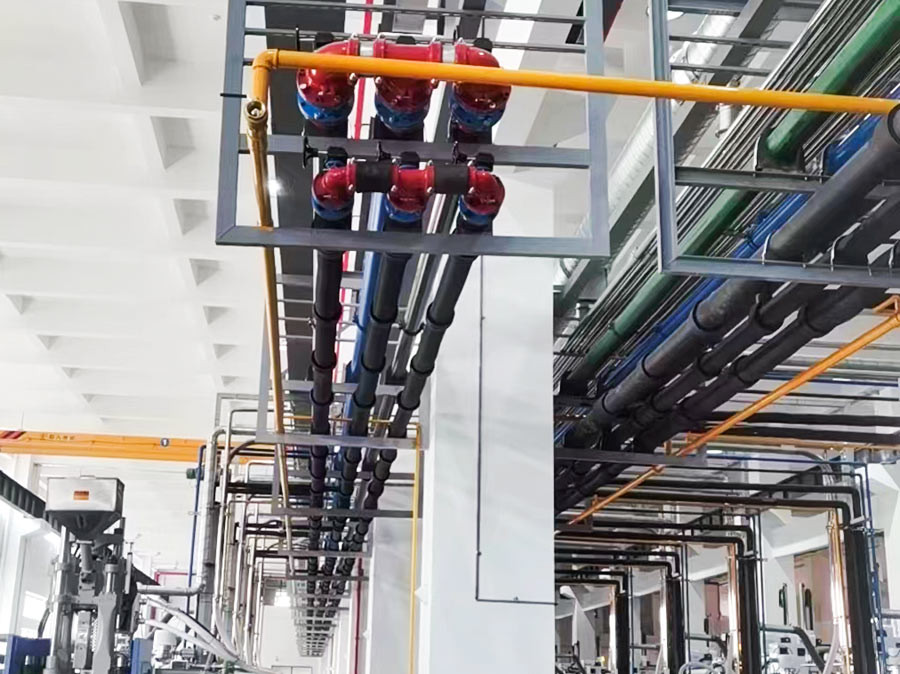
The pump group is connected by groove parts, which have good extensibility (such as increasing pumps) and facilitate the pump disassembly and installation during repair for quick maintenance. When the number of machines in the workshop exceeds the planned flow on demands, the backup pump can also be automatically started as per workshop load.
The entire system adopts the same return water to ensure equal pressure difference at each water station. The surface of the chilled water pipeline in the workshop is covered with insulated cotton can not only provide a balanced cold water temperature but also avoid condensation on the pipeline surface; All outdoor pipelines are covered with insulated cotton, and the external layer is covered with an aluminum sheet to prevent rust and corrosion and ensure system long-term and reliable operation.
Central Material Processing System
The central material processing system helps the customers reduce manpower and management costs through its advantages of automated operations and centralized management features, thus improving space utilization. Meanwhile, the clean and sound workshop environment enhances the factory’s image.
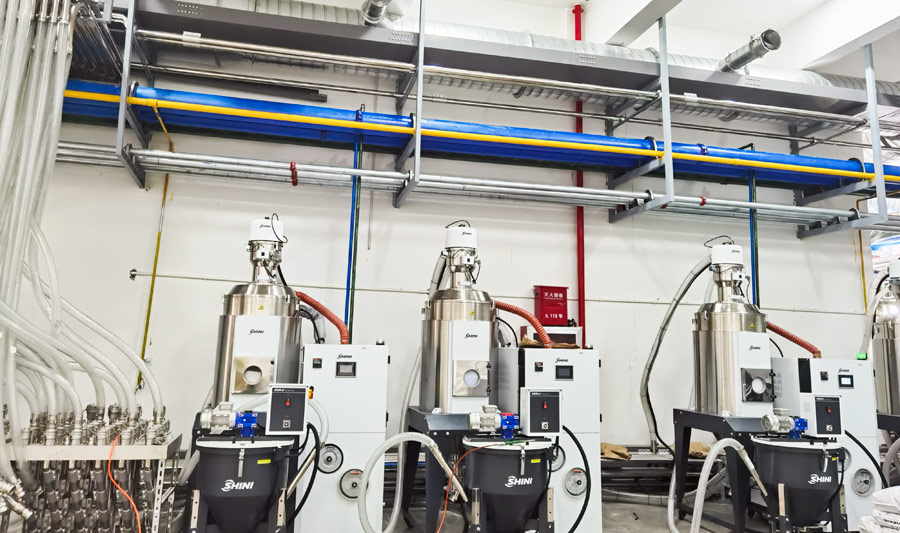
The central material processing system enables centralized materials management by zones independent of the injection moulding workshop. There are material areas, soundproof rooms, and several dehumidifying and drying equipment in the feeding area. The feeding section adopts a centralized feeding and conveying system of a single machine and single pipe, collocating with a shared pipeline for backup. It is equipped with a high-pressure blower to provide the conveying power and a central filter to filtrate the dust and fine impurities in the materials, thus effectively protecting the blower and extending its service life. The soundproof room for blowers vastly reduces the noise during operation.
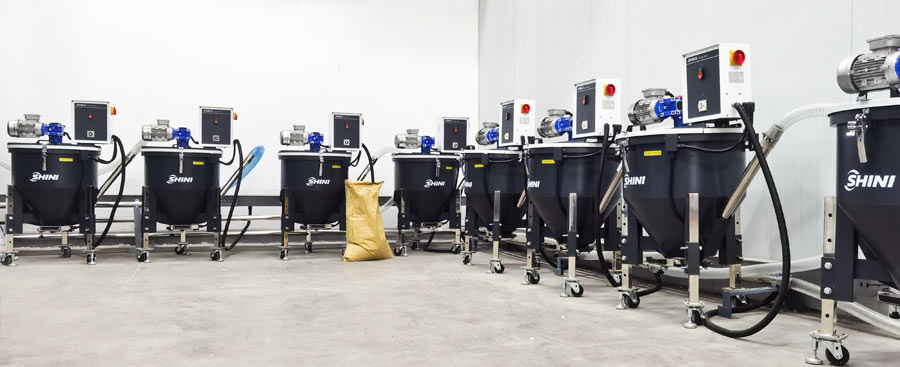
In the storage section, it utilizes a Euro mixing MST to meet the mixing demands of the customer while storing the materials. In the drying selection, it is equipped with a Hopper Dryer and a Dehumidifying Dryer that can efficiently dry most non-hygroscopic plastics to ensure the quality of final products. The dehumidifying dryer mainly processes highly hygroscopic plastics and collocated with material distribution stations and PLC control stations for centralized drying, dehumidifying, and conveying of materials.
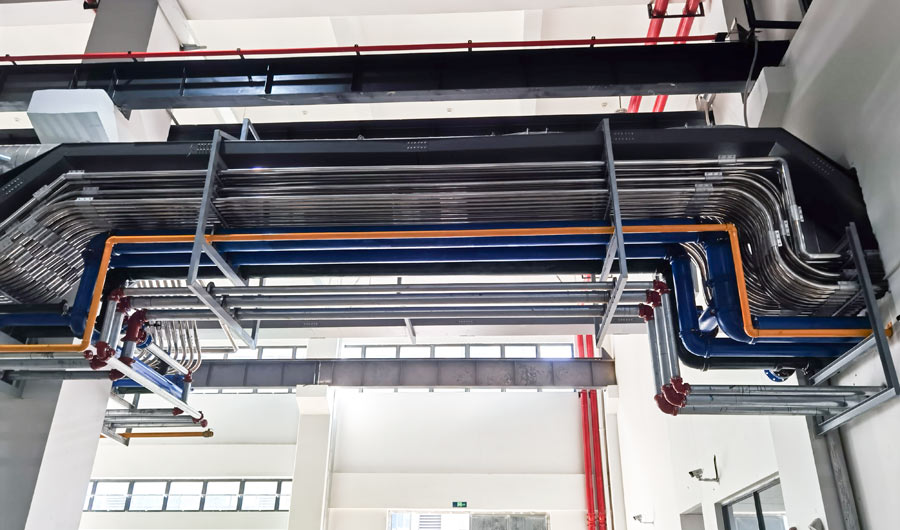
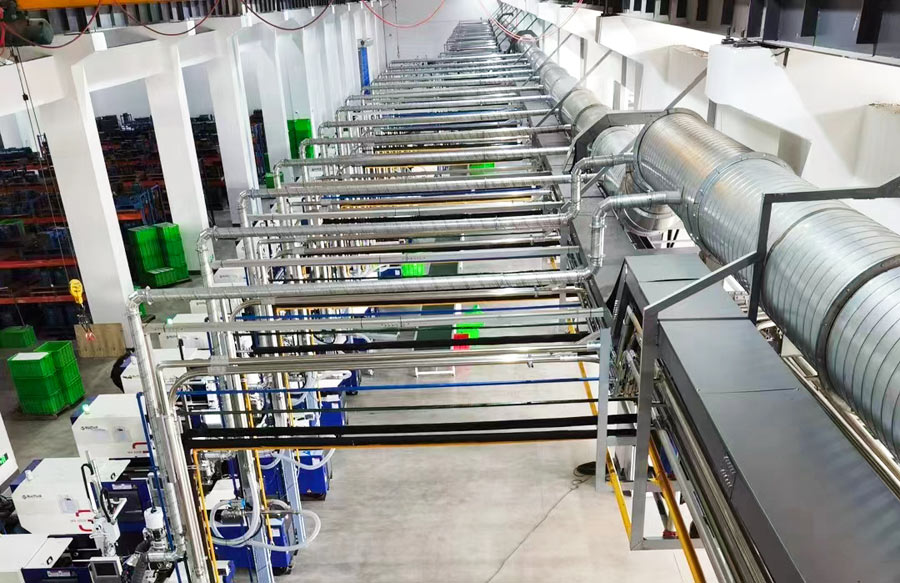
For the pipeline layout, whole columns of the workshop are used as the pipe support for fixation, featuring a well-arranged and neat design. Considering the installation distance, the terminal pipeline with stainless steel columns is separately planned. In addition, the loader installed on the injection moulding machine at the end of conveying system is additionally equipped with a proportional valve to meet the mixing demands of the customer.
In practical use, customers can observe the operation of various equipment in real-time by the touch screen of the PLC control station, which can cooperate with the material distribution station's material selection function to switch the materials. Different pipeline equipment is designed with identifications for easy use and selection.
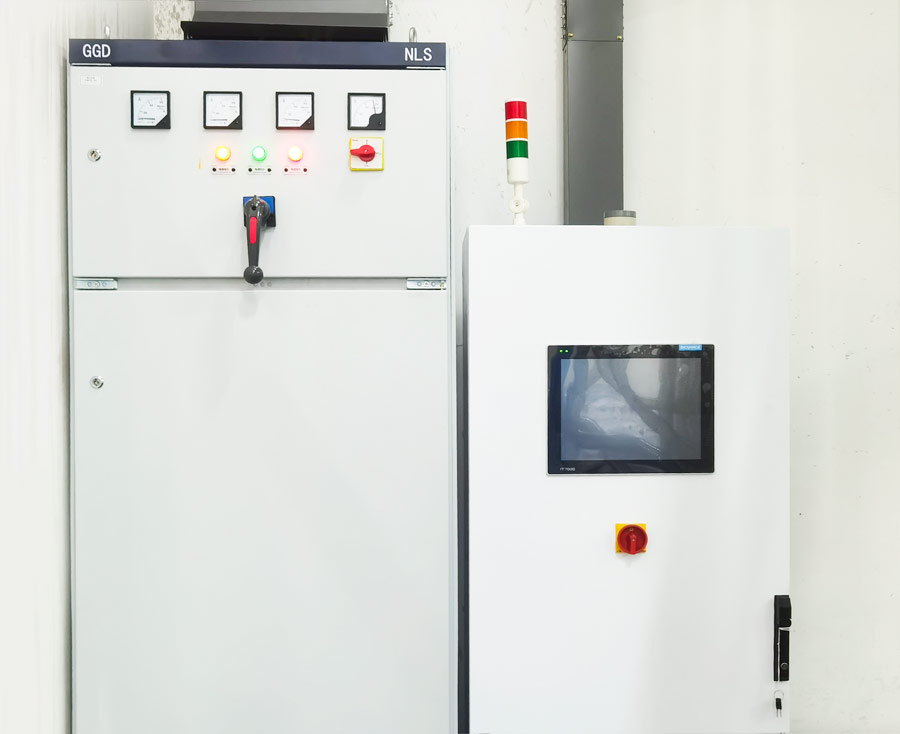
From the selection to layout design, this whole plant planning perfectly shows the system’s integrity and conforms to the intelligent manufacturing trend. Shini will always stand at the front of the industry tendency. The system has been put into production, and the customer has fully recognized its performance and reliability.
Relying on her advantages, Shini has successfully delivered many water and electrical systems in the market and gained valuable experiences to provide customers with a more professional and complete set of products. Established in Taiwan in 1969, Shini has experienced over 50 years of development and become an international plastic material handling equipment manufacturer that integrates scientific research, manufacturing, sales, and service in one. It has won multiple honors such as "National Famous Trademark", "specialized and new ‘Little Giant’ enterprise", "Top Five Enterprise in China Plastic Auxiliary Machinery Industry", "National High-tech Enterprise", "National Intellectual Property Demonstration Enterprise", "China Patent Award", and so on. Besides, it is also the vice-chairman unit of the China Plastic Machine Industry Association and a member unit of the China Plastics Association Injection Moulding Products Special Committee.
Experience Sharing
If you want to read other articles, back to2023 Quarter 2 Issue 50.