Experience Sharing
2022 Quarter 3 Issue 48
Centralize Material Processing Systems in Photovoltaic Industry
The photovoltaic energy business is a high-tech enterprise founded in 2010 that engaged in research and development, production, and sales of solar energy system-related materials. According to the characteristics, manufacturing processes of the product, and on-site survey, Shini has provided the customer with a complete set of steady and reliable centralized material handling systems.
The system is based on the existing four rows of 88 injection moulding machines with a clamping force between 160t~260t, mainly using PA, PPO, and PPE materials and some glass fiber-contained materials to produce photovoltaic energy products.
Energy saving improves the efficiency for steady and reliable operation.
Energy saving improves the efficiency for steady and reliable operation.
The production is designed with four sets of blowers. Each blower services 22 units of injection moulding machine, and it significantly saves energy consumption compared with individual material loading units.
To reduce investment and avoid waste, the team fully uses the existing 42 units of vacuum hopper receivers by integrating them into the system with diaphragm valve modification. The plan replaces the individual hot air dryer with nine sets of large dryers SHD-E in the material room. Compared with the dryer with each injection moulding machine, the centralized dryers has dramatically improved the ambient condition in the production, reduced the noise, and increased the space utilization rate.
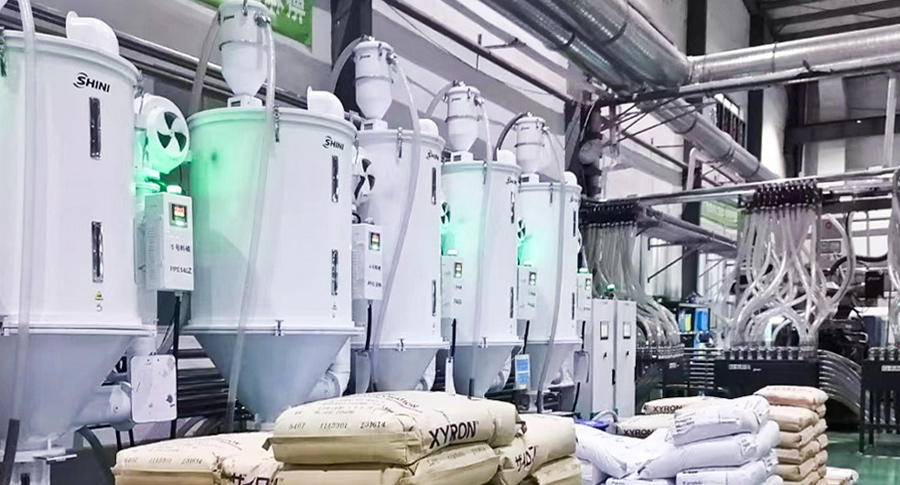
Material auto distribution makes operation flexible
There are shut-off suction boxes with multiple pipes at the bottom of the dryer. It works with the material distribution station that not only achieves greater flexible alternative switching between multi-channels and routes of materials but also ensures no residues during long-distance conveying to avoid material contamination and waste. The well-designed material distribution station, considering wear resistance and pipeline matching, can meet the production demand of any material selected by up to 88 sets of machines. The same material can be used by 32 machines in the workshop simultaneously.
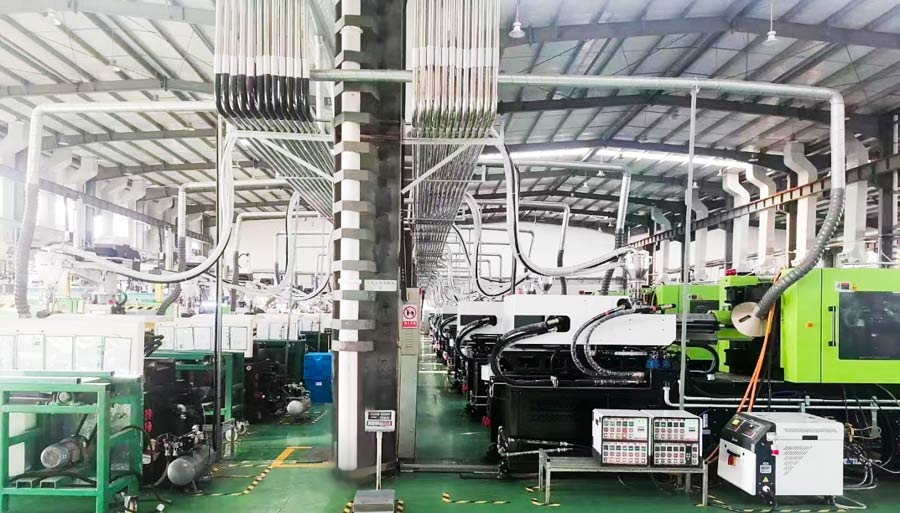
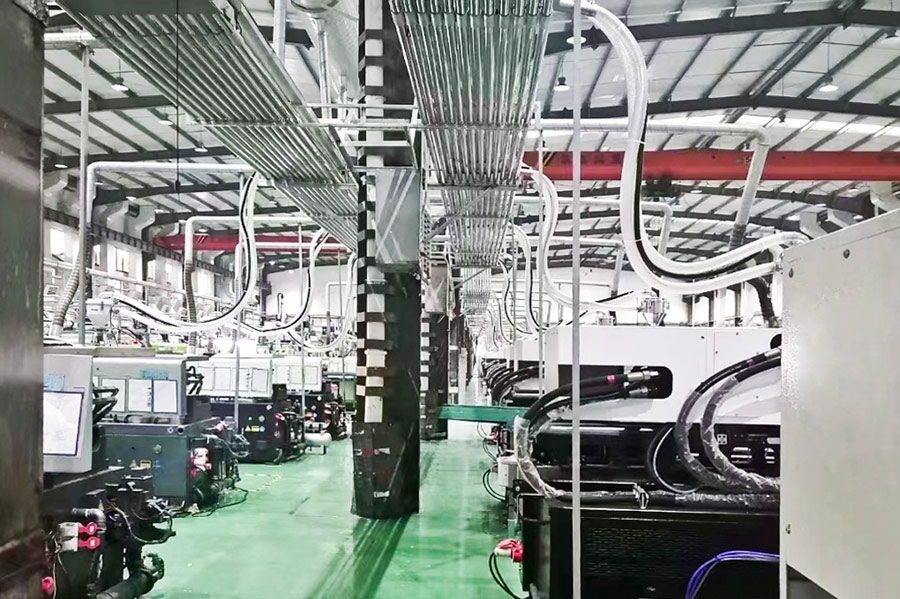
Customer Feedback
The customer has highly affirmed the system since its completion. That improves the injection moulding process in all aspects, which the centralized project has also approved in the photovoltaic energy industry.
The system is based on the existing four rows of 88 injection moulding machines with a clamping force between 160t~260t, mainly using PA, PPO, and PPE materials and some glass fiber-contained materials to produce photovoltaic energy products.
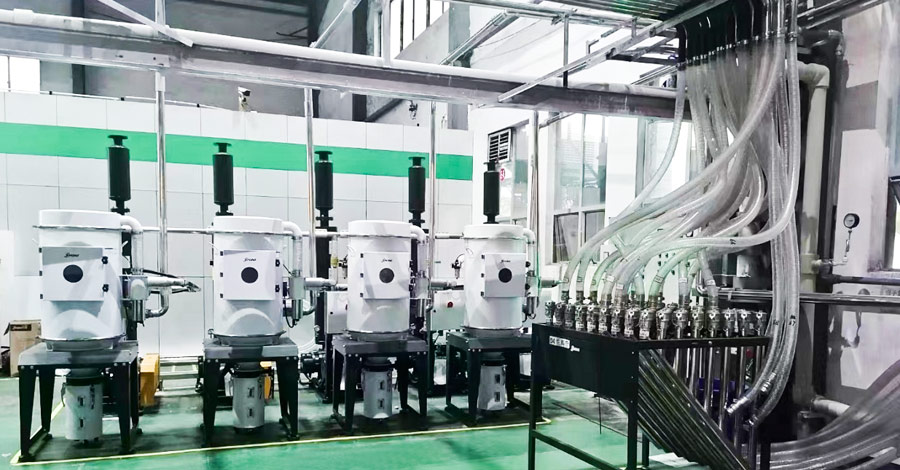
Energy saving improves the efficiency for steady and reliable operation.
Energy saving improves the efficiency for steady and reliable operation.
The production is designed with four sets of blowers. Each blower services 22 units of injection moulding machine, and it significantly saves energy consumption compared with individual material loading units.
To reduce investment and avoid waste, the team fully uses the existing 42 units of vacuum hopper receivers by integrating them into the system with diaphragm valve modification. The plan replaces the individual hot air dryer with nine sets of large dryers SHD-E in the material room. Compared with the dryer with each injection moulding machine, the centralized dryers has dramatically improved the ambient condition in the production, reduced the noise, and increased the space utilization rate.
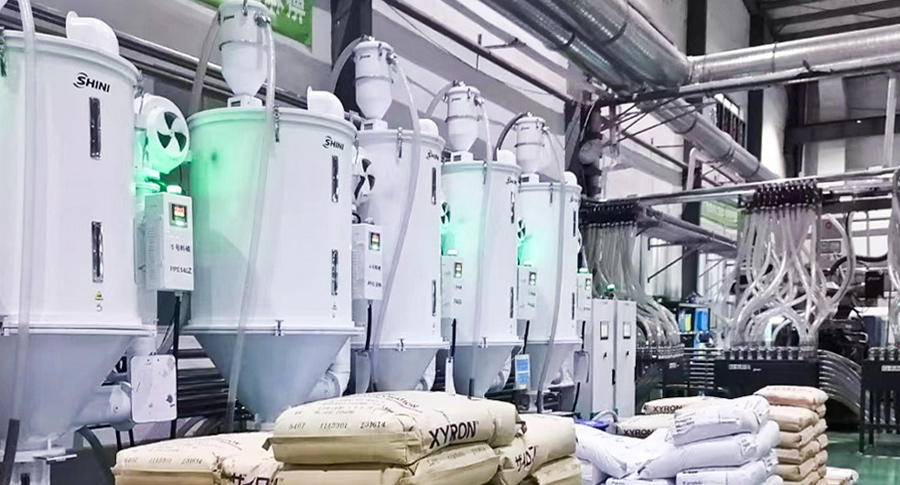
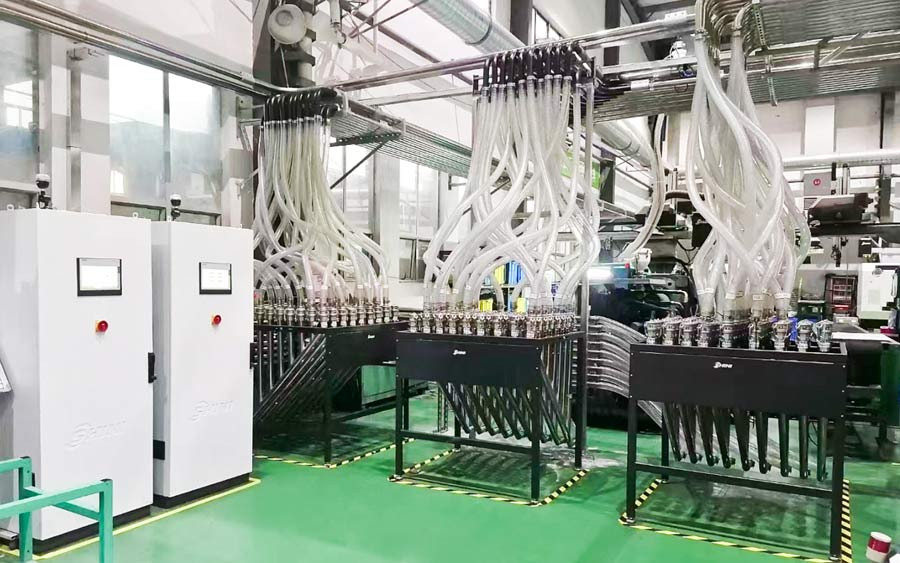
Material auto distribution makes operation flexible
There are shut-off suction boxes with multiple pipes at the bottom of the dryer. It works with the material distribution station that not only achieves greater flexible alternative switching between multi-channels and routes of materials but also ensures no residues during long-distance conveying to avoid material contamination and waste. The well-designed material distribution station, considering wear resistance and pipeline matching, can meet the production demand of any material selected by up to 88 sets of machines. The same material can be used by 32 machines in the workshop simultaneously.
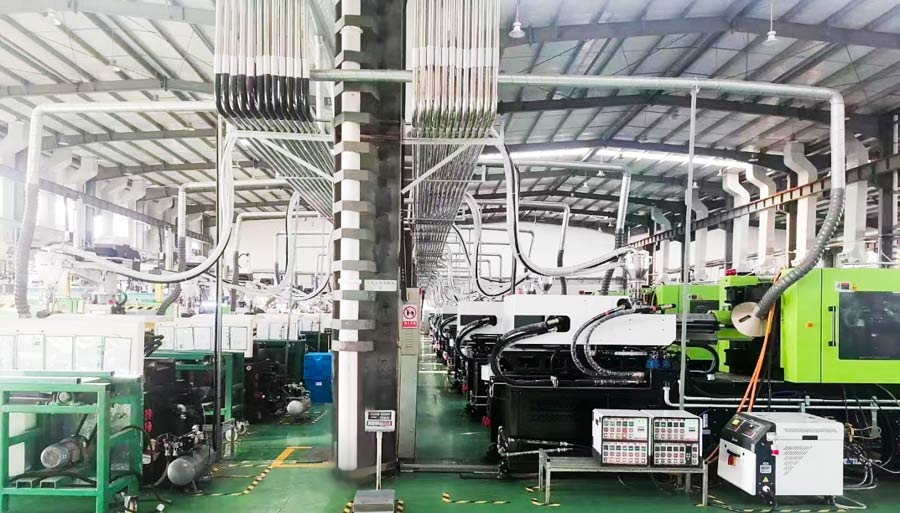
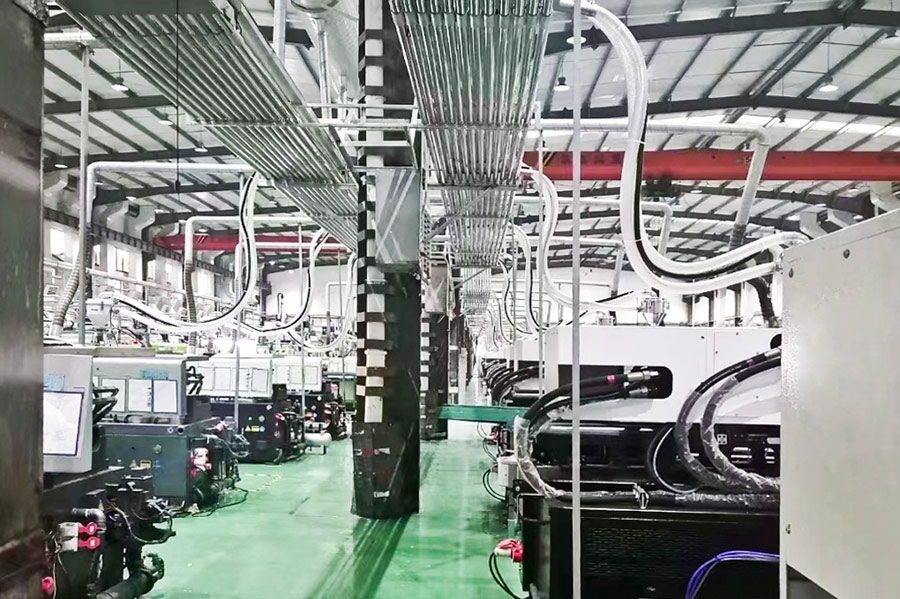
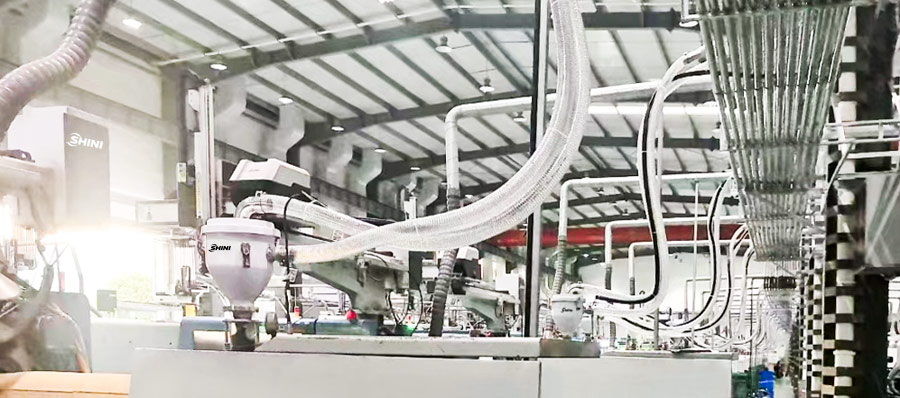
Customer Feedback
The customer has highly affirmed the system since its completion. That improves the injection moulding process in all aspects, which the centralized project has also approved in the photovoltaic energy industry.
Experience Sharing
- Smart Home Appliance Industry with touch of Automated Solution
- Energy Efficient, Smart Modular Dehumidifying Dryer
If you want to read other articles, back to2022 Quarter 3 Issue 48.