Special Reports
2022 Quarter 3 Issue 48
A Step of Mould Flow Detection Plays A Decisive Role in Production
How is the mould temperature being controlled? Generally speaking, a constant temperature medium is sent into the mould water loop to regulate and control the mould temperature. A large mould or complex injection process can equip multiple temperature control units to handle the different mould temperatures by the zone. Therefore, the mould temperature is constantly kept indirectly by medium circulation with an external mould temperature unit. As the medium circulates in the water loop, circulating medium pressure and flow are critical for maintaining mould temperature. Especially for precision injection moulding products or large-scale injection moulding products, the temperature uniformity and distribution can determine whether the products are qualified.
So how to monitor the medium flow in the mould effectively?
There are methods to measure the mould water flow. A visual water distributor or a flow meter in the piping to measure the medium flow in real-time. For conventional visible water distributors, visible parts of the pipes are made of PC materials, and the maximum working temperature is usually not more than 100 ℃. It can read the flow according to the scale on the pipe. However, using a flow meter to measure the flow, its working temperature can reach 300℃ and meet most of the process requirements. A flow meter will display the real-time flow data on the screen for intuitive data inquiry. When the mould pipe is blocked, it's difficult for conventional visual water flow regulators to alarm and give feedback on the abnormalities in time. It usually requires the operator to check the flow regularly. In the flow meter design, flow abnormality can be quickly feedback to the controller, informing the operator in time, which essentially guarantees the mould temperature maintenance for reliable production. The flow data can be collected via a communication port for future production needs or QC documentation.
Shini offers various flow metering solutions for your production needs
According to different production and process requirements, Shini provides diverse mould flow measuring solutions for the customers to meet their customized applications.
Select the equipment with flow detection function
Select an optional or customized flow sensor on the mould temperature unit. For example, the water heater STM-W has the option of adding a flow meter, which can add a flow sensor in the circulating loop, and its maximum working temperature can reach 120 ℃. Besides the high-temperature water heater, STM-SPW has a standard flow metering, and the unit's max working temperature is 200℃. Both units can measure the circulating loop's total flow in real-time, set the alarm threshold value, and prompt the flow abnormality in time. Other oil temperature control units or water chillers can also select and adapt to various customized flow metering solutions in different applications.
SIFR Intelligent Flow Regulator
The SIFR intelligent flow regulator is mainly used to monitor the medium flow and temperature of each mould loop and can work with the mould temperature control unit, water chiller, or circular cooling water. Meanwhile, it can connect with multiple mould connectors, and the touch screen can display circulating water flow and temperature synchronously in real-time, with the maximum working temperature reaching 160 ℃, and manually control the flow. Moreover, a standard alarm function can set different alarm values for each water loop and give real-time feedback on the alarm information. Also, the machine has a communication interface, which can upload valuable information, such as flow, temperature, and alarm, to other intelligent systems as required, including injection moulding machine, extruder, and MES system, thus achieving data interconnection, sharing, tracing and analysis, and improving the real-time data utilization.

Water Flow Regulator
The SFR water flow distributor can provide multi-channel distribution of water flow according to technical requirements, which can conveniently adjust and check the flow and temperature of each water loop. The modular design dramatically facilitates the water loop expansion and maintenance. Besides, mechanical structural design can select appropriate supports and pipe joints according to different demands, without energy consumption to meet the needs of different occasions.
So how to monitor the medium flow in the mould effectively?
There are methods to measure the mould water flow. A visual water distributor or a flow meter in the piping to measure the medium flow in real-time. For conventional visible water distributors, visible parts of the pipes are made of PC materials, and the maximum working temperature is usually not more than 100 ℃. It can read the flow according to the scale on the pipe. However, using a flow meter to measure the flow, its working temperature can reach 300℃ and meet most of the process requirements. A flow meter will display the real-time flow data on the screen for intuitive data inquiry. When the mould pipe is blocked, it's difficult for conventional visual water flow regulators to alarm and give feedback on the abnormalities in time. It usually requires the operator to check the flow regularly. In the flow meter design, flow abnormality can be quickly feedback to the controller, informing the operator in time, which essentially guarantees the mould temperature maintenance for reliable production. The flow data can be collected via a communication port for future production needs or QC documentation.
Shini offers various flow metering solutions for your production needs
According to different production and process requirements, Shini provides diverse mould flow measuring solutions for the customers to meet their customized applications.
Select the equipment with flow detection function
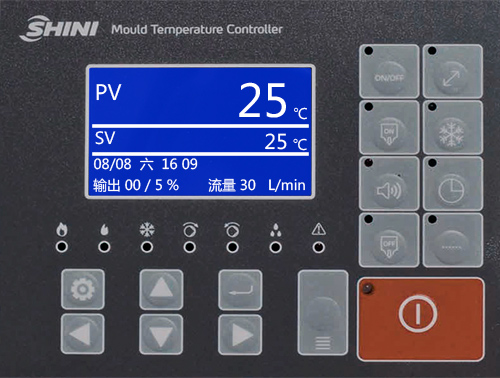
Select an optional or customized flow sensor on the mould temperature unit. For example, the water heater STM-W has the option of adding a flow meter, which can add a flow sensor in the circulating loop, and its maximum working temperature can reach 120 ℃. Besides the high-temperature water heater, STM-SPW has a standard flow metering, and the unit's max working temperature is 200℃. Both units can measure the circulating loop's total flow in real-time, set the alarm threshold value, and prompt the flow abnormality in time. Other oil temperature control units or water chillers can also select and adapt to various customized flow metering solutions in different applications.
SIFR Intelligent Flow Regulator
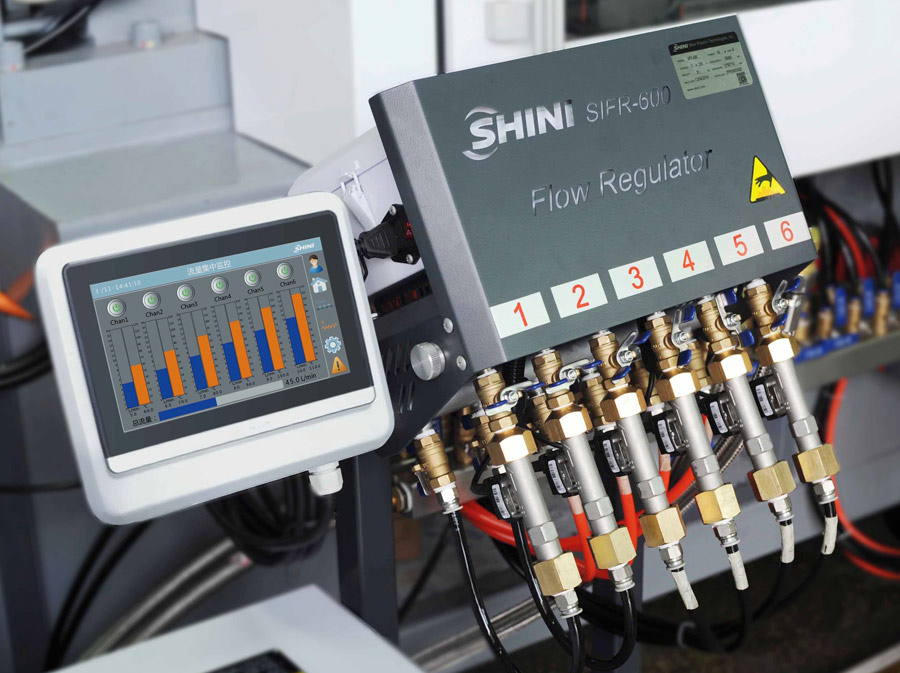
The SIFR intelligent flow regulator is mainly used to monitor the medium flow and temperature of each mould loop and can work with the mould temperature control unit, water chiller, or circular cooling water. Meanwhile, it can connect with multiple mould connectors, and the touch screen can display circulating water flow and temperature synchronously in real-time, with the maximum working temperature reaching 160 ℃, and manually control the flow. Moreover, a standard alarm function can set different alarm values for each water loop and give real-time feedback on the alarm information. Also, the machine has a communication interface, which can upload valuable information, such as flow, temperature, and alarm, to other intelligent systems as required, including injection moulding machine, extruder, and MES system, thus achieving data interconnection, sharing, tracing and analysis, and improving the real-time data utilization.

Water Flow Regulator
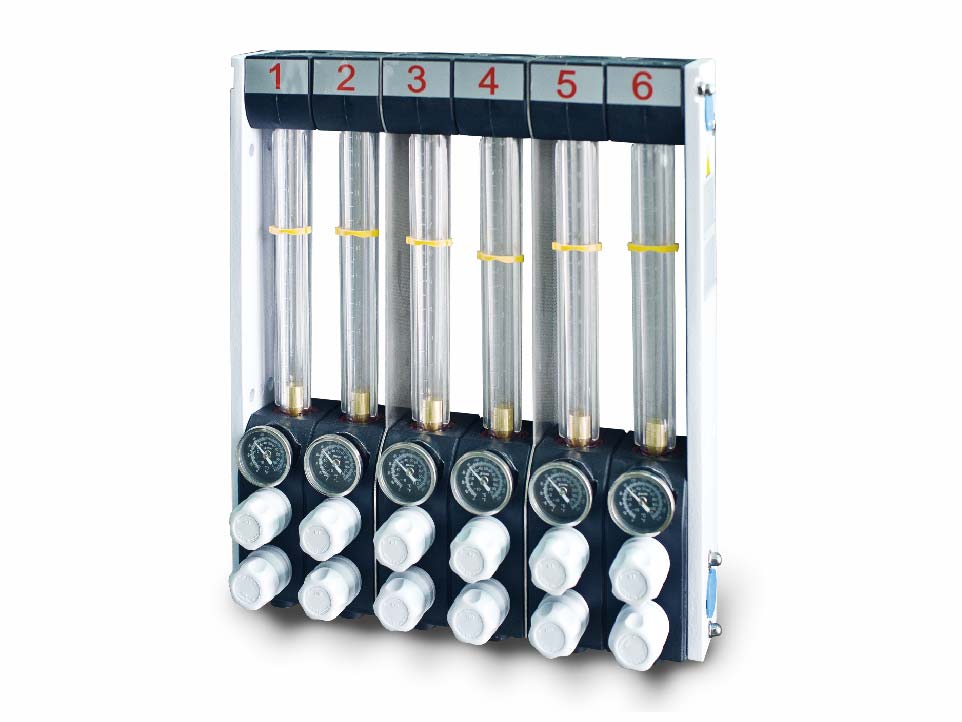
The SFR water flow distributor can provide multi-channel distribution of water flow according to technical requirements, which can conveniently adjust and check the flow and temperature of each water loop. The modular design dramatically facilitates the water loop expansion and maintenance. Besides, mechanical structural design can select appropriate supports and pipe joints according to different demands, without energy consumption to meet the needs of different occasions.
Special Reports
- Large Bulk Conveying Made Simple, Pressure Conveying.
- Shini @ VietnamPlas 2022
- ShiniEurope Quarterly 2022 No.2
- ShiniEurope Quarterly 2022 No.3
If you want to read other articles, back to2022 Quarter 3 Issue 48.